31 กรกฏาคม 2566: อาจารย์ ดร.ไมตรี บุญขันธ์ ได้ฝึกอบรมหลักสูตร… “เทคนิคการวิเคราะห์และแก้ไขปัญหาด้วย Why Why Analysis” ครับ
ขอบคุณ บริษัท จีจีซี เคทิส ไบโออินดัสเทรียล จำกัด ด้วยครับ
การดำเนินกิจกรรมแก้ไขปัญหาในการทำงานด้วยตนเอง หรือ Self-Solving problem นั้นมีหลักการที่ใช้ดำเนินการที่จะทำให้การแก้ไขปัญหานั้นมีประสิทธิภาพอย่างมาก นั้นก็คือ หลักการ 5 Gen ประกอบไปด้วย Genba , Genbutsu , Genjitsu , Genri และ Gensoku ซึ่งทั้ง 5 หลักการนี้เป็นสิ่งแรกที่ควรให้ความสำคัญอย่างยิ่ง โดย 3G แรก นั้นสำคัญกับการดำเนินการ ค้นหาปัญหา เป็นการลงไปเห็นที่จุดเกิดเหตุเองนั้น เป็นสิ่งที่สำคัญเพราะการหาสิ่งผิดปกติ เพื่อนำไปแก้ไขและปรับปรุงให้ดีขึ้น ไม่ใช่นั่งเทียนเขียนขึ้นมาหลักการ 3 Gen ที่ว่าคือ
Genba แปลไทย: สถานที่ / หน้างานจริง หมายถึง การลงไปสำรวจที่หน้างานจริง
Genbutsu แปลไทย: สิ่งของ/ชิ้นงานที่เป็นตัวปัญหาจริง หมายถึง การดูสังเกตและจับต้องชิ้นงานที่ผลิตได้จริงหรือตัวสินค้าที่จัดเก็บอยู่จริงหรือชิ้นงานที่กำลังถูกตรวจสอบอยู่
Genjitsu แปลไทย: สถานการณ์จริง หมายถึง เหตุการณ์หรือสถานการณ์ที่เกิดปัญหาจริง เช่น สภาพแวดล้อมหรือกระบวนการ ขั้นตอนการทำงานหรือช่วงเวลาที่ผลิตของเสียบ่อยๆ หรือที่เกิดปัญหาได้บ่อย ๆ
เมื่อผ่านการใช้หลักการ 3 Gen แล้วหากอยากเห็นเป็นรูปธรรมต้องใช้การขับเคลื่อนโดยผ่าน Small group Activity ได้แก่ One Point Lesson , กิจกรรม QCC โดยการทำกิจกรรมเหล่านี้เป็นการยืนยันให้เห็นเป็นรูปธรรมมากที่สุด เพราะการติดตามงานของหัวหน้างานและดูความคืบหน้าของกิจกรรมที่ทำ หรือง่ายๆจะเข้าใจในรูปแบบ PDCA เพื่อทำให้เกิดความชัดเจนว่า
“ ขณะนี้จะต้องทำอะไรบ้าง ”
“ มีปัญหาอะไรอยู่บ้าง “
“ แก้ไขแล้วเป็นอย่างไรบ้าง ”
และเมื่อการดำเนินการแก้ไขปัญหาเริ่มใช้อย่างเต็มที่ จะใช้หลักการวิเคราะห์ โดยหลักการ 2 Gen ที่เหลือคือ
Genri แปลไทย: ทฤษฎีที่เกี่ยวข้องจริง หมายถึง หลักการที่ใช้ในการทำงาน หรือมาตรฐานการผลิตในปัจจุบัน, สมมุติฐานในการแก้ไขหรือตรวจสอบ สูตรการผลิต หรือส่วนประกอบในการผลิตที่ใช้อยู่ในปัจจุบัน
Gensoku แปลไทย: เงื่อนไขประกอบที่เกี่ยวข้องจริง หมายถึง ข้อจำกัด ข้อตกลง หรือกฎที่บังคับใช้อยู่ในปัจจุบัน
ด้วยเหตุผลนี้เองการที่เราลงพื้นที่หน้าจริง สถานที่จริง เจอของจริง จะทำให้เราสามารถตัดสินใจและเข้าใจปัญหาอย่างแท้จริง และท้ายที่สุดก็จะพัฒนาการทำงานสู่รูปแบบ Daily Management เพื่อเป็นสร้างให้งานที่ทำประจำให้ได้ตามภารกิจและเป้าหมายที่วางไว้ หากไม่ได้ตามเป้าหมายก็ต้องมีการปรับปรุง
หลักสูตรนี้จึงเป็นคำตอบที่ดีของการใช้เครื่องมือในการแก้ไขปัญหาการทำงานได้อย่างเป็นระบบและเห็นผลได้อย่างแน่นอน เป็นการรวบรวมเครื่องมือที่ใช้แก้ไขปัญหากับพนักงานในระดับปฏิบัติการและฝึกการรวมกลุ่มทำกิจกรรมเพื่อช่วยกันระดมสมอง ในการแก้ไขปัญหาได้เป็นอย่างดีอีกด้วย นอกจากการเรียนรู้เทคนิคการวิเคราะห์ปัญหาแล้ว ผู้ปฏิบัติงานควรได้เรียนรู้ถึงเครื่องมือต่าง ๆ ที่ใช้ในการบริหารการผลิตเพื่อเพิ่มประสิทธิภาพการผลิตอย่างสมบูรณ์แบบ เช่น เทคนิคการวิเคราะห์สาเหตุตามหลัก 4M (สาเหตุของปัญหาจาก คน, เครื่องจักร, วัตถุดิบ และวิธีการ) เทคนิคในการตัดสินใจเลือกวิธีในการแก้ไขในระดับต่าง เช่น การแก้ไขปัญหาระยะสั้น ระยะกลาง และการวางแผนแก้ไขในอนาคต รวมถึงเทคนิคการวิเคราะห์ผลกระทบที่อาจส่งผลต่อการผลิต เป็นต้น ก็จะพบการเปลี่ยนแปลงในการปฏิบัติงานไปในทางที่ดีขึ้นได้อย่างแน่นอน เช่นลดต้นทุนการผลิต ลดปัญหาความเสียหาย ลดความสูญเปล่าจากการแก้ไขการรอคอยงาน การขาดประสิทธิภาพในการปฏิบัติงานและยังสามารถสร้างแรงจูงใจในการทำงานให้กับบุคลากรภายในได้
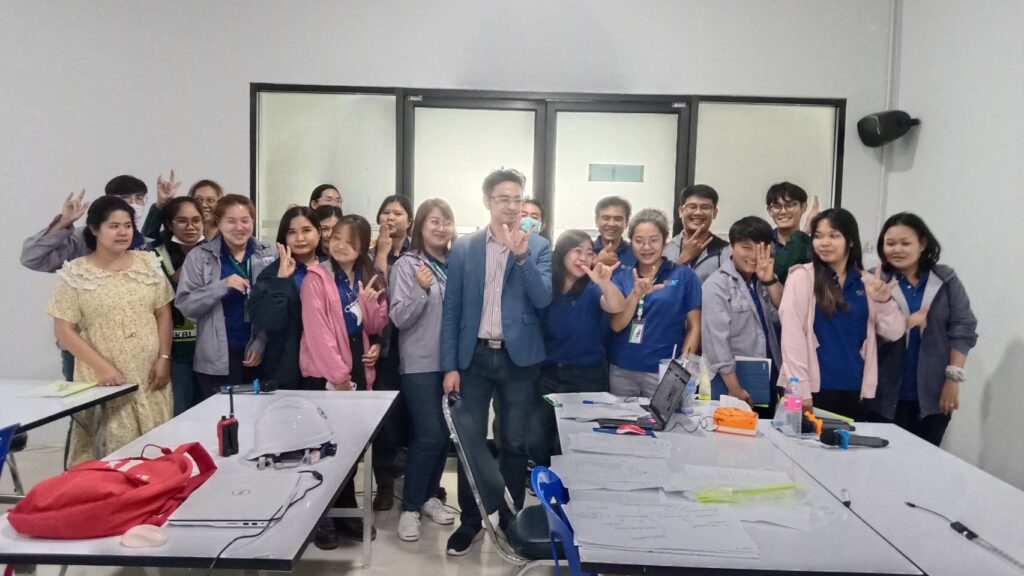
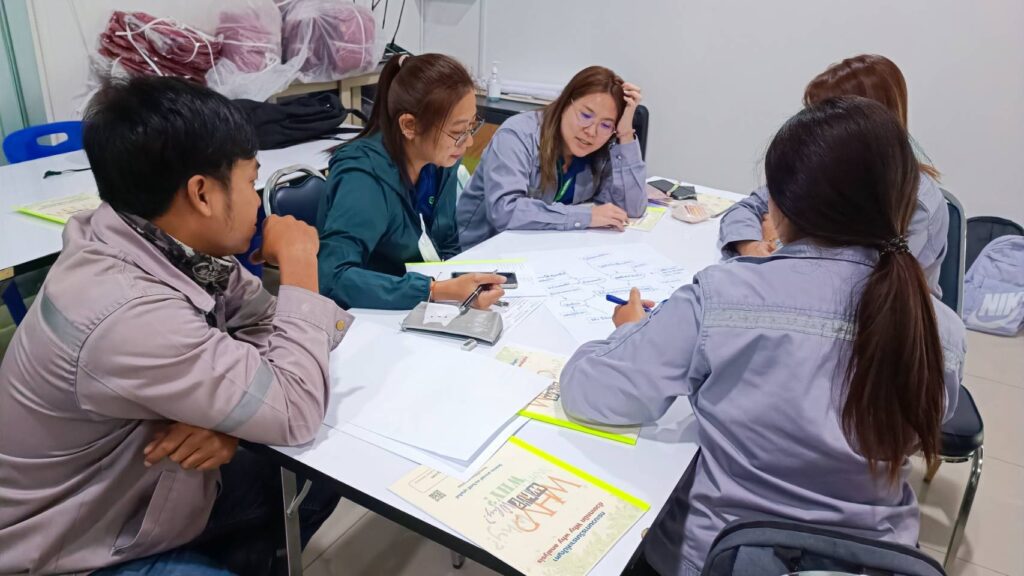
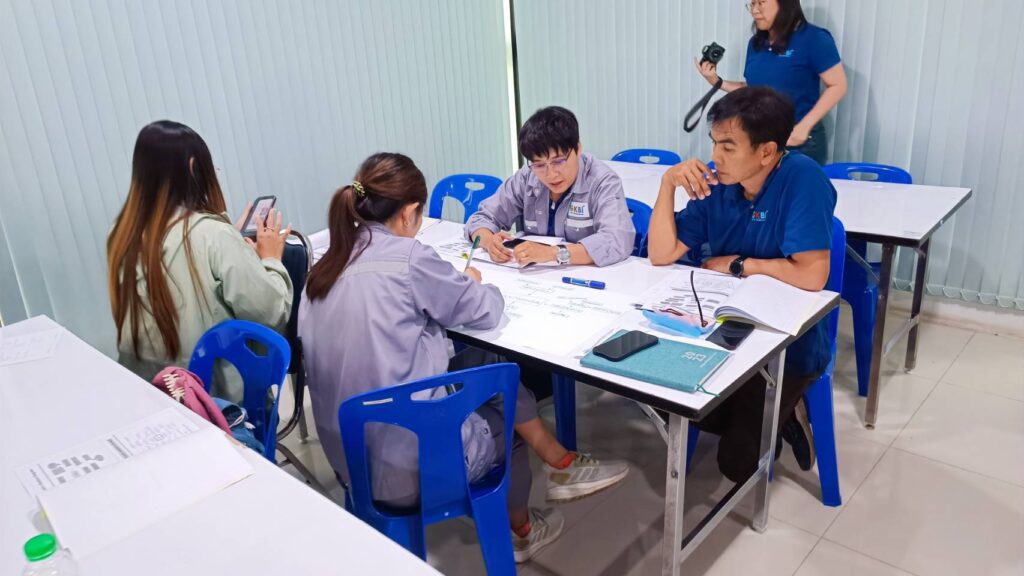
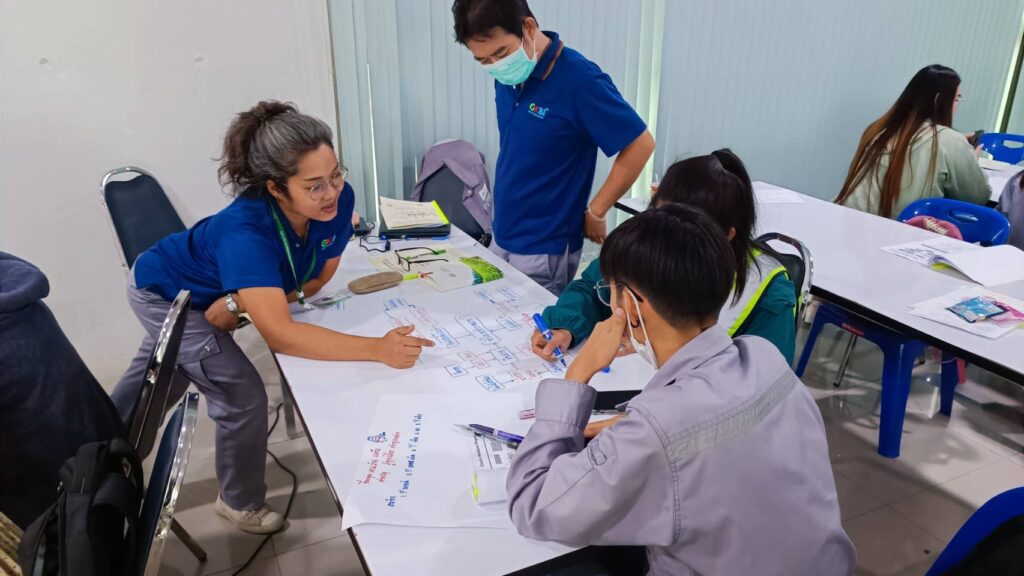
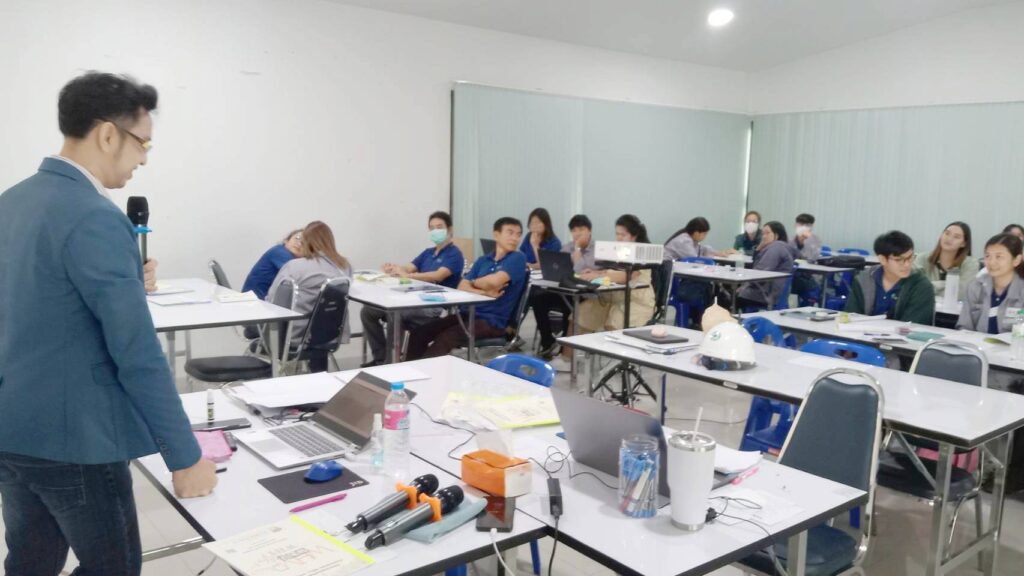
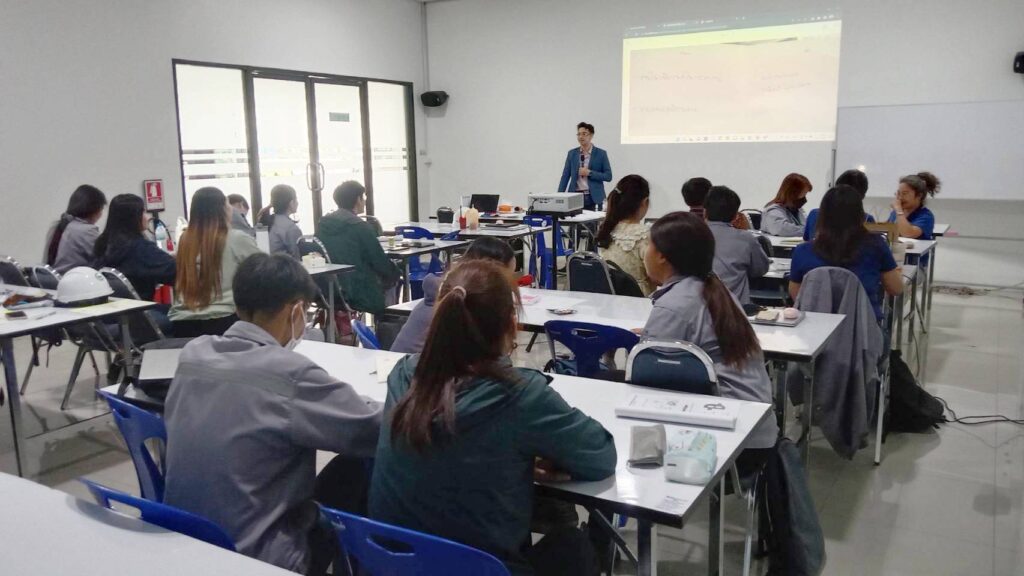
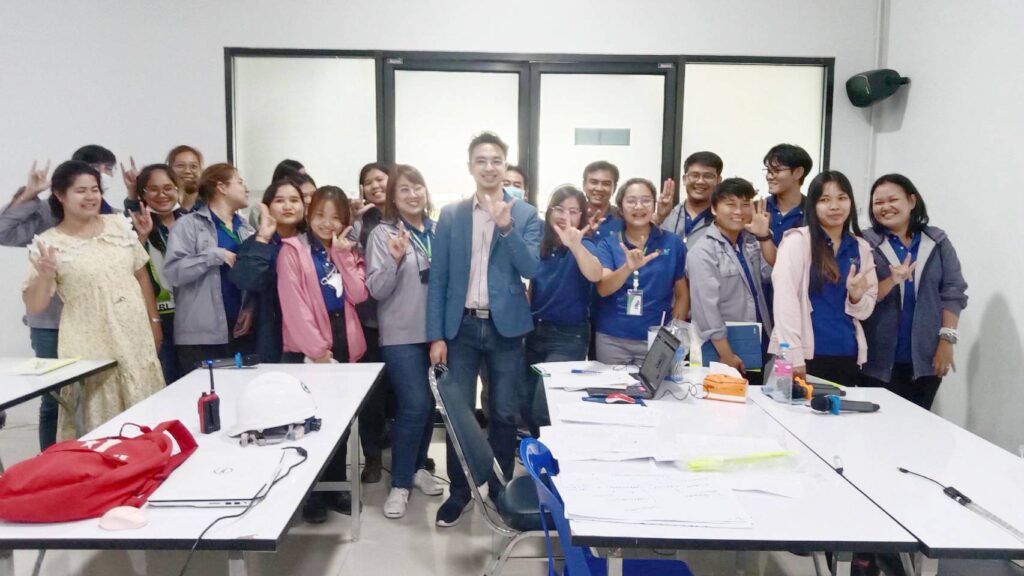
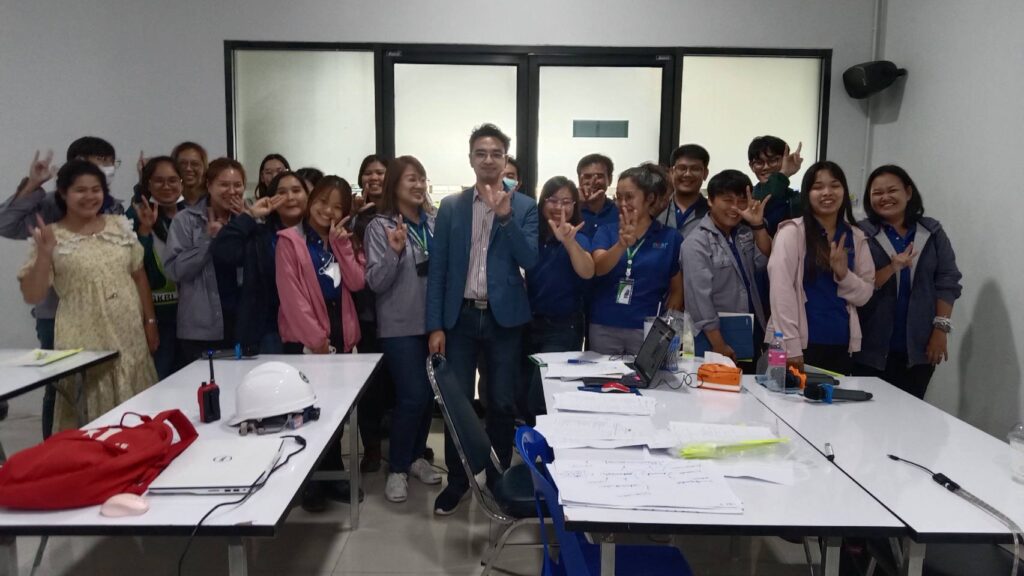
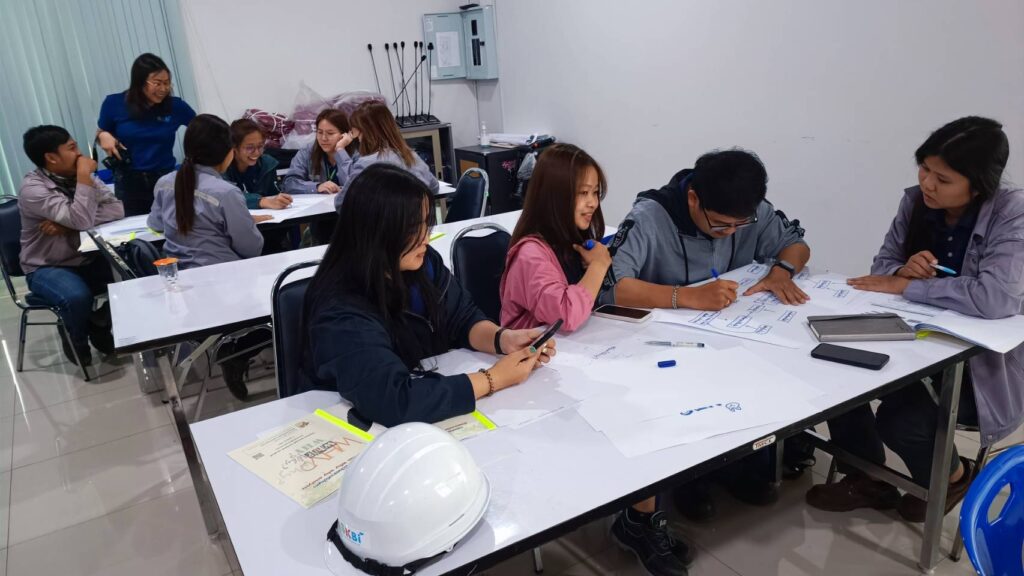
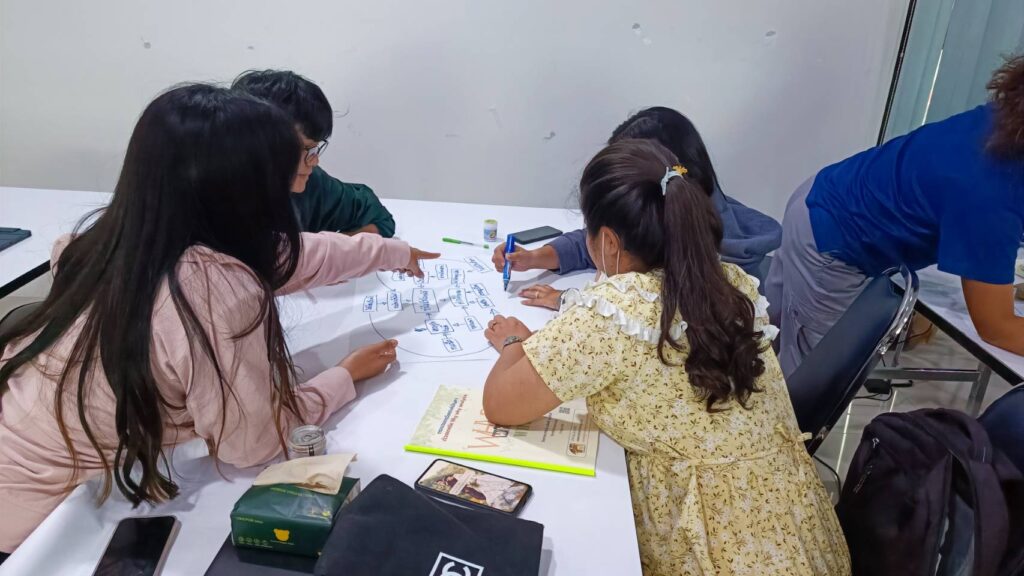
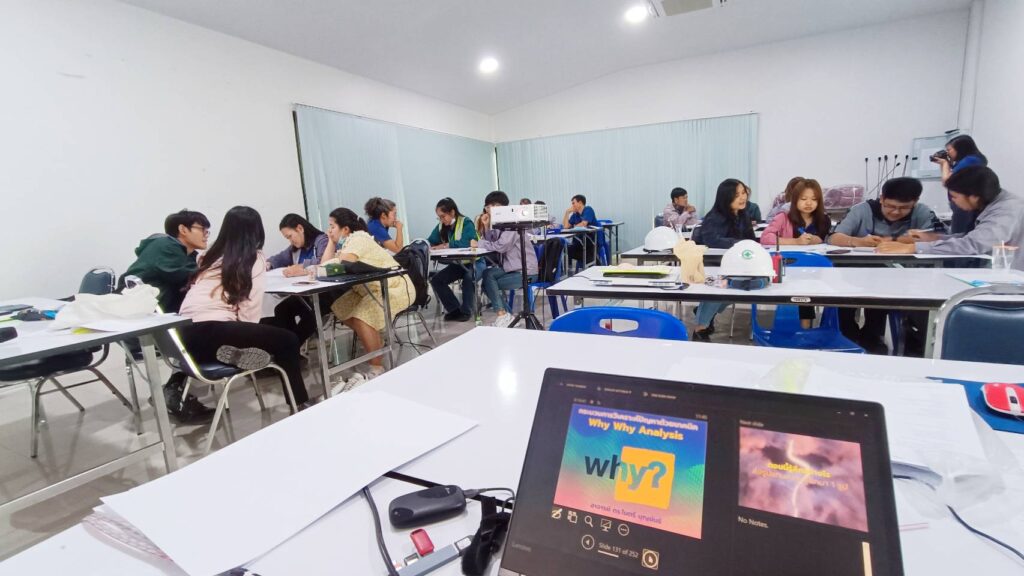
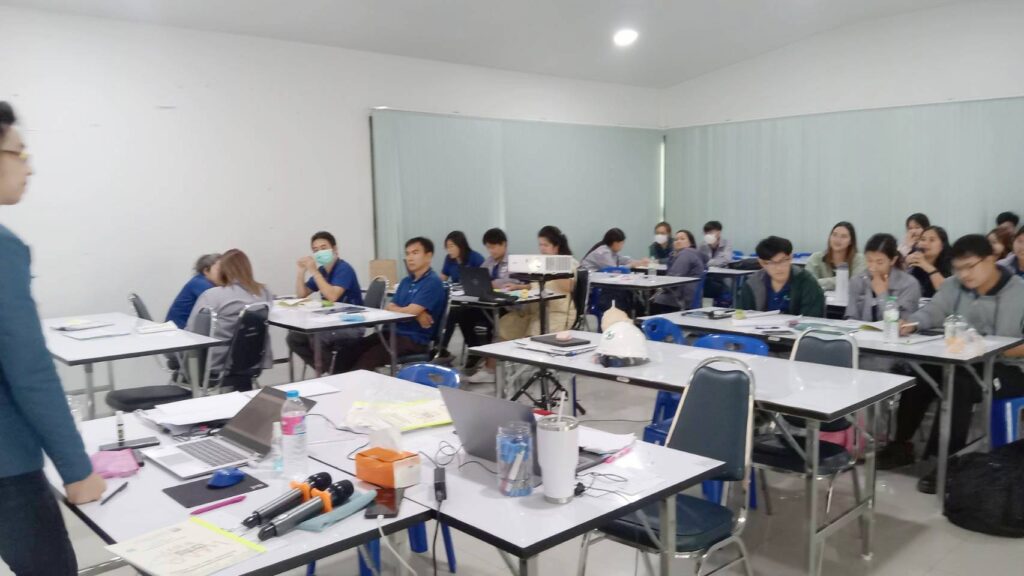