16 มิถุนายน 2566: อาจารย์ไมตรี บุญขันธ์ ได้อบรมในหลักสูตร..🎉🎊✈ “การลดต้นทุนและกำจัดความสูญเปล่า 7 ประการ (7 Waste) “ 💓🎄🌿 ครับ
ขอบคุณ บริษัท จีจีซี เคทิส ไบโออินด้สเทรียล จํากัด ด้วยครับ
การดำเนินธุรกิจในปัจจุบัน เป็นการแข่งขันในการลดต้นทุนการผลิตเพื่อเพิ่มประสิทธิภาพในการทำงานและเพิ่มคุณภาพให้กับสินค้า ทำให้สามารถได้กำไรในการผลิตที่เพิ่มขึ้น ซึ่งง่ายกว่าการขึ้นราคาสินค้ามาก เทคนิคการลดต้นทุนทั้งในและนอกกระบวนการผลิตมีอยู่หลายวิธี MUDA MURI MURA
เป็นเทคนิคแนวคิดของประเทศญี่ปุ่นในการบริหารงาน Muda หรือความสูญเปล่า อาจเกิดได้หลายลักษณะ เช่น ความสูญเปล่าที่เกิดจากการรอ การเคลื่อนย้าย การปรับเปลี่ยน การทำใหม่ การถกเถียง ความสูญเปล่าทั้ง 8 ประการ (7+1 wastes)
ความสูญเปล่าที่ 1 ความสูญเสียที่เกิดจากการผลิตมากเกินไป (Overproduction)
ความสูญเปล่าที่ 2 ความสูญเสียที่เกิดจากการผลิตของเสีย (Defect)
ความสูญเปล่าที่ 3 ความสูญเสียที่เกิดจากการล่าช้าหรือการรอคอย (Delay or Waiting)
ความสูญเปล่าที่ 4 ความสูญเสียที่เกิดจากการมีวัสดุคงคลังที่ไม่จำเป็น (Inventory / working – process)
ความสูญเปล่าที่ 5 ความสูญเสียที่เกิดจากการขนส่งหรือขนย้าย (Transport)
ความสูญเปล่าที่ 6 ความสูญเสียเกิดจากการกระบวนการผลิต (Process)
ความสูญเปล่าที่ 7 ความสูญเสียที่เกิดจากการเคลื่อนไหวที่ไม่จำเป็น (Motion)
ตามทฤษฎีเดิม 7 wastes ได้มีเพิ่มความสูญเปล่าตัวที่ 8 (ความสูญเปล่า 7+1 ประการ)
ความสูญเปล่าที่ 8 การใช้คนไม่เป็น (Underutilized people)
Mura หรือความไม่สม่ำเสมอ งานที่มีความไม่สม่ำเสมอไม่ว่าจะเป็นในเรื่องปริมาณงาน ทำให้เกิดความไม่สม่ำเสมอของผลงานตามไปด้วย และความไม่มีมาตรฐานของการทำงาน
Muri หรือการฝืนทำ การฝืนทำสิ่งใด ๆ ก็ตามมักทำให้เกิดผลกระทบบางอย่างในระยะยาว
สรุปคือ MUDA ความสูญเปล่าที่เกิดขึ้น MURI ความยากลำบากความไม่เป็นธรรมชาติ และ MURA ความไม่สม่ำเสมอในการทำงาน ความหมายรวมคือการเปรียบเทียบระหว่าง จุดประสงค์ (สิ่งที่ต้องการ) กับวิธีการ (วิธีที่จะทำให้ได้ในสิ่งที่ต้องการ) วิธีการต่างเกินไปน้อยเกินไปหรือไม่สม่ำเสมอก็จะทำให้เกิดความสูญเปล่าได้ทั้งสิ้น ดังนั้นจำเป็นอย่างยิ่งที่จะต้องปูพื้นฐานความรู้ความเข้าใจถึงสาเหตุดังกล่าวข้างต้น ว่าจะมีแนวทางป้องกันแก้ไขด้วยวิธีการง่ายๆ ได้อย่างไรและสามารถนำไปประยุกต์ปฏิบัติใช้ได้อย่างมีประสิทธิผลเกิดประสิทธิภาพการทำงานของพนักงานเพิ่มขึ้น
หลักสูตรนี้จึงเป็นคำตอบที่ดีของการใช้เครื่องมือในการแก้ไขปัญหาการทำงานได้อย่างเป็นระบบและเห็นผลได้อย่างแน่นอน เป็นการรวบรวมเครื่องมือที่ใช้แก้ไขปัญหากับพนักงานในระดับปฏิบัติการและการรวมกลุ่มทำกิจกรรมเพื่อช่วยกันระดมสมอง ในการแก้ไขปัญหาด้วยหลักการ 7 Waste เป็นอย่างดีอีกด้วย
หัวข้อการอบรม
- หลักการดำเนินธุรกิจอุตสาหกรรมและงานบริการในปัจจุบัน
- “กำไร” ขององค์กรเกิดขึ้นจากสิ่งใด
- ความหมายและความสำคัญของคำว่า “ต้นทุน”
- ความท้าทายที่จำเป็นต้องมุ่งเน้นที่ “ความสูญเสีย”
- ความหมายของหลักการลดต้นทุนด้วย “7 Waste’
- แนวความคิดหลักเกี่ยวกับความสูญเปล่าและต้นทุน
ความสูญเปล่าที่ 1 ความสูญเสียที่เกิดจากการผลิตมากเกินไป (Overproduction)
ความสูญเปล่าที่ 2 ความสูญเสียที่เกิดจากการผลิตของเสีย (Defect)
ความสูญเปล่าที่ 3 ความสูญเสียที่เกิดจากการล่าช้าหรือการรอคอย (Delay or Waiting)
ความสูญเปล่าที่ 4 ความสูญเสียที่เกิดจากการมีวัสดุคงคลังที่ไม่จำเป็น (Inventory / working – process)
ความสูญเปล่าที่ 5 ความสูญเสียที่เกิดจากการขนส่งหรือขนย้าย (Transport)
ความสูญเปล่าที่ 6 ความสูญเสียเกิดจากการกระบวนการผลิต (Process)
ความสูญเปล่าที่ 7 ความสูญเสียที่เกิดจากการเคลื่อนไหวที่ไม่จำเป็น (Motion)
ตามทฤษฎีเดิม 7 wastes ได้มีเพิ่มความสูญเปล่าตัวที่ 8 (ความสูญเปล่า 7+1 ประการ)
ความสูญเปล่าที่ 8 การใช้คนไม่เป็น (Underutilized people) - เทคนิคการวิเคราะห์ความสูญเสียด้วย Flow diagram อย่างง่าย
- การประยุกต์ใช้เครื่องมือ ไคเซ็น, Visual control และ Poka Yoke เพื่อลดความสูญเสีย
- เทคนิคของการปรับปรุงงานอย่างต่อเนื่องด้วยหลัก PDCA เพื่อลดความสูญเปล่าในการทำงาน
- ตัวอย่างต่างๆ ที่ประสบความสำเร็จในการลด Waste ขององค์กรอื่นๆ
Work Shop1 “ระดมสมองเพื่อวิเคราะห์ความสูญเสียในการทำงาน”
Work Shop2 “ใจเขาใจเรากับคุณภาพที่ลูกค้าต้องการ”
Work Shop3 “มาสร้างเป้าหมายการทำงานร่วมกันด้วยการทำงานเป็นทีม”
-แลกเปลี่ยนเรียนรู้ถามตอบ
กลุ่มเป้าหมาย
หัวหน้างาน พนักงาน และผู้ที่สนใจทั่วไป
รูปแบบการสัมมนา
- การบรรยาย 50 %
- เกมส์ / กิจกรรมกลุ่ม / ฝึกปฏิบัติ Workshop และการนำเสนอผลงานกลุ่ม 40%
- กรณีศึกษา และดูภาพยนตร์ 10 %
ประโยชน์ที่คาดว่าจะได้รับ
1.ผู้เข้าอบรมสามารถเรียนรู้และเข้าใจหลักการวิเคราะห์ปัญหาอย่างถูกต้อง
2.ผู้เข้าอบรมสามารถนำหลักการขจัด 7 Waste ไปประยุกต์ใช้กับงานของตนเองได้อย่างมีประสิทธิภาพ
3.ผู้เข้าอบรมสามารถเรียนรู้การทำงานร่วมกับผู้อื่น
4.ผู้เข้าอบรมมีจิตสำนึกเรื่องคุณภาพและทำงานอย่างมีประสิทธิภาพ
5.ผู้เข้าอบรมมีความรู้กับการทำกิจกรรมลดต้นทุนการผลิตในองค์กรมากขึ้น

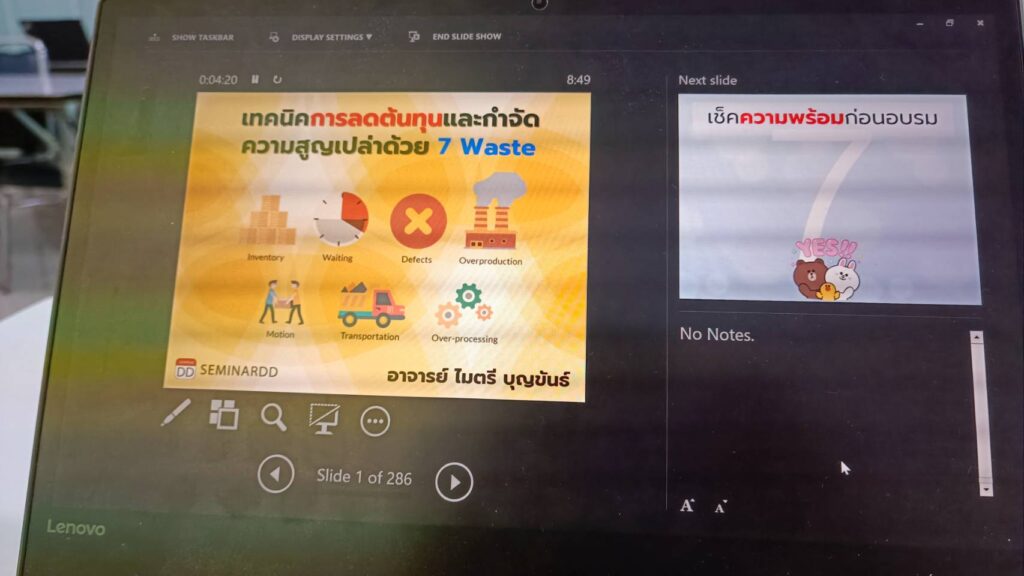
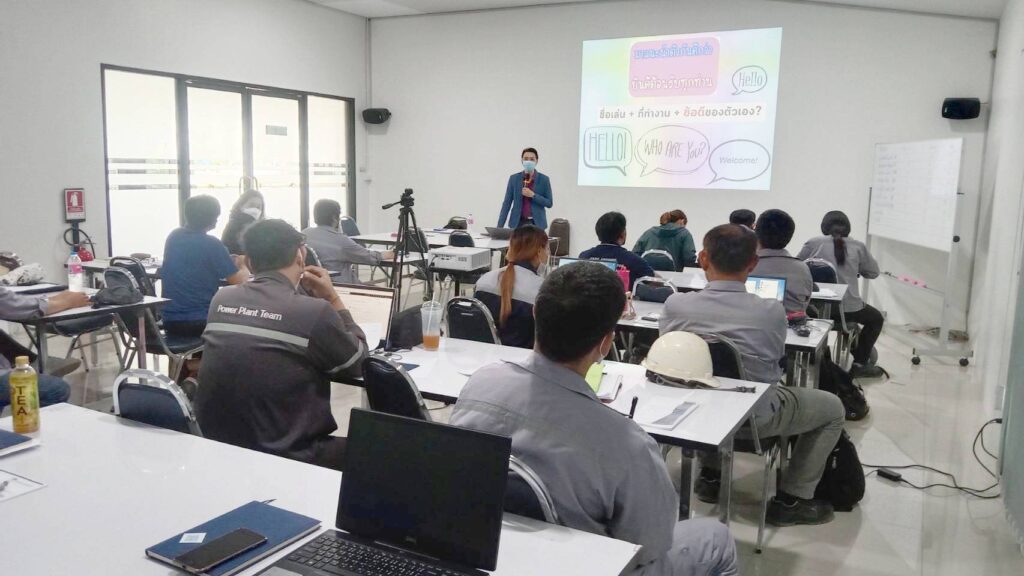
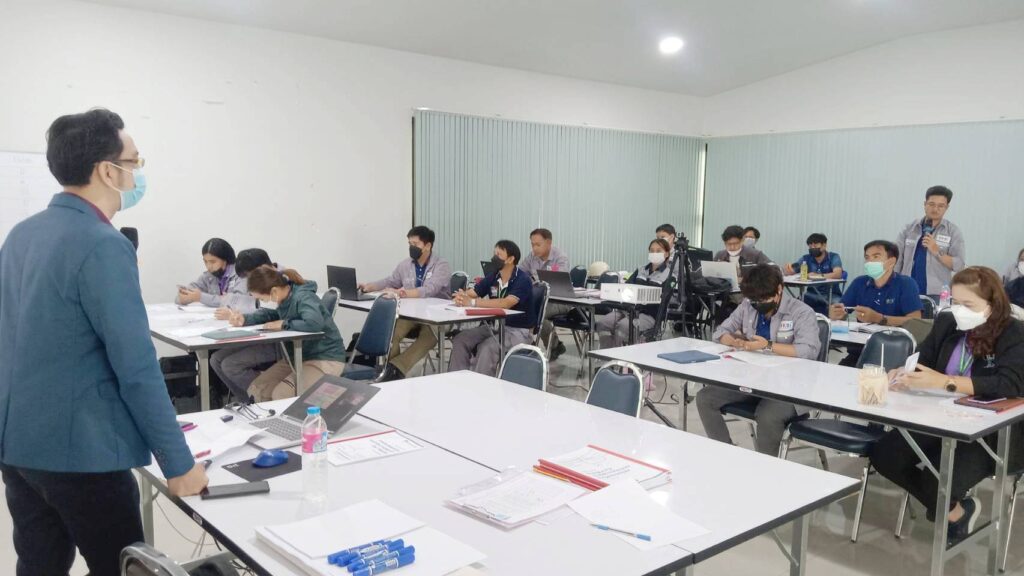
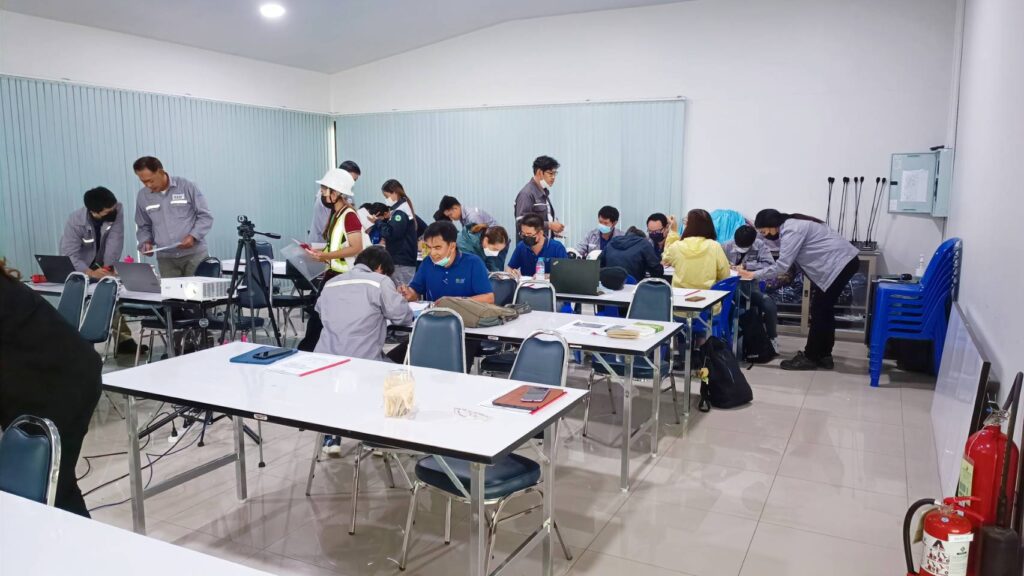
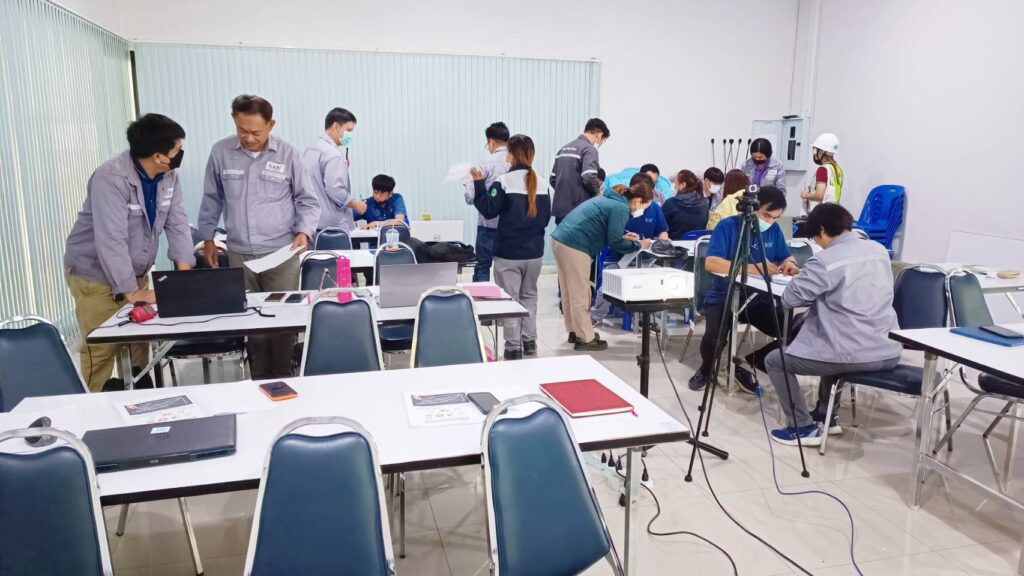
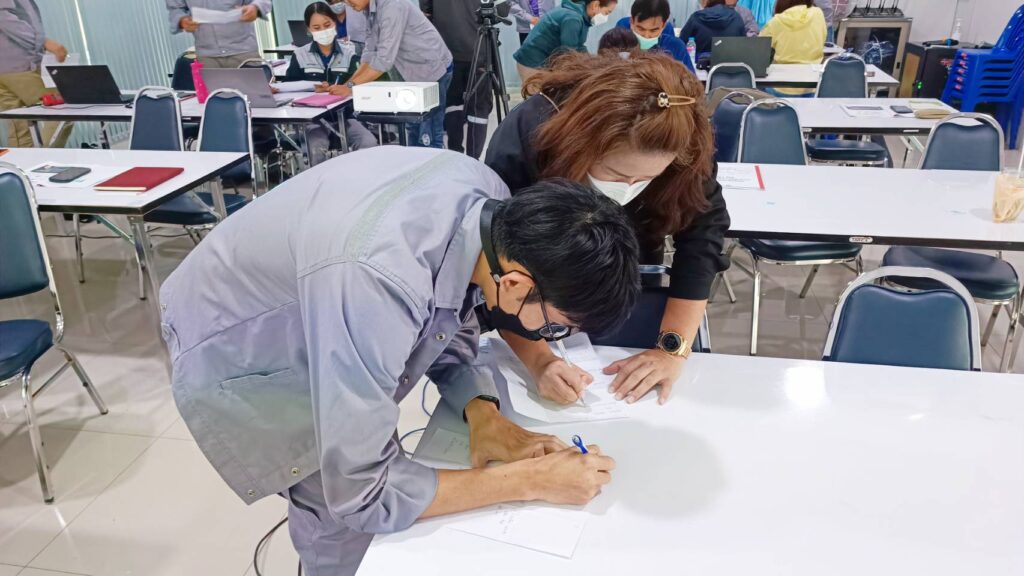
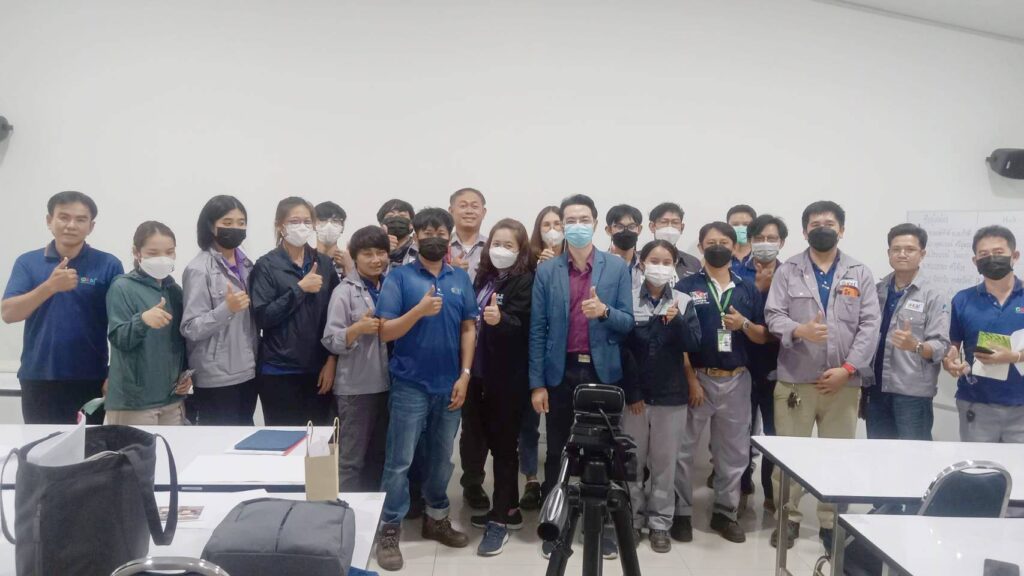
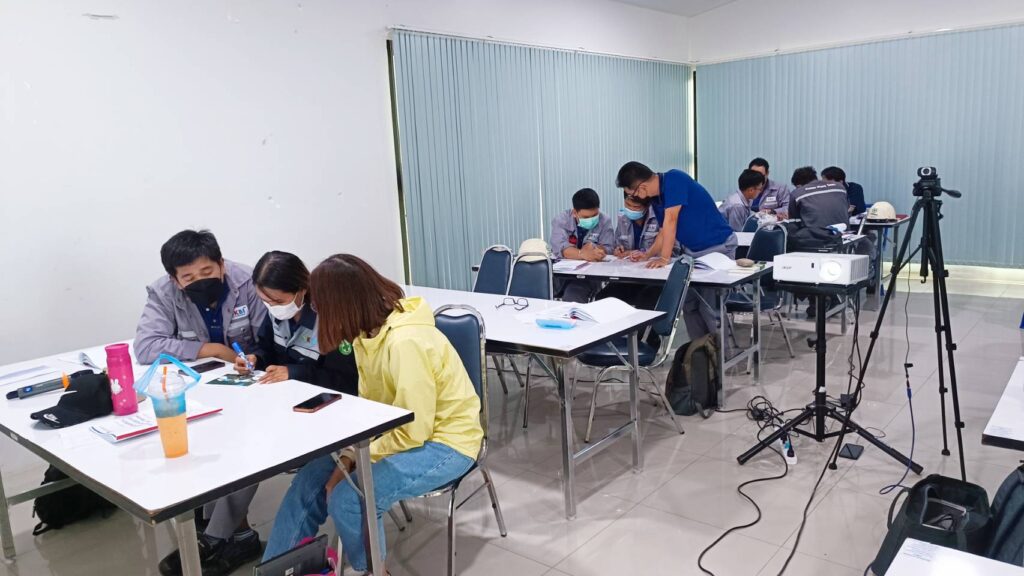
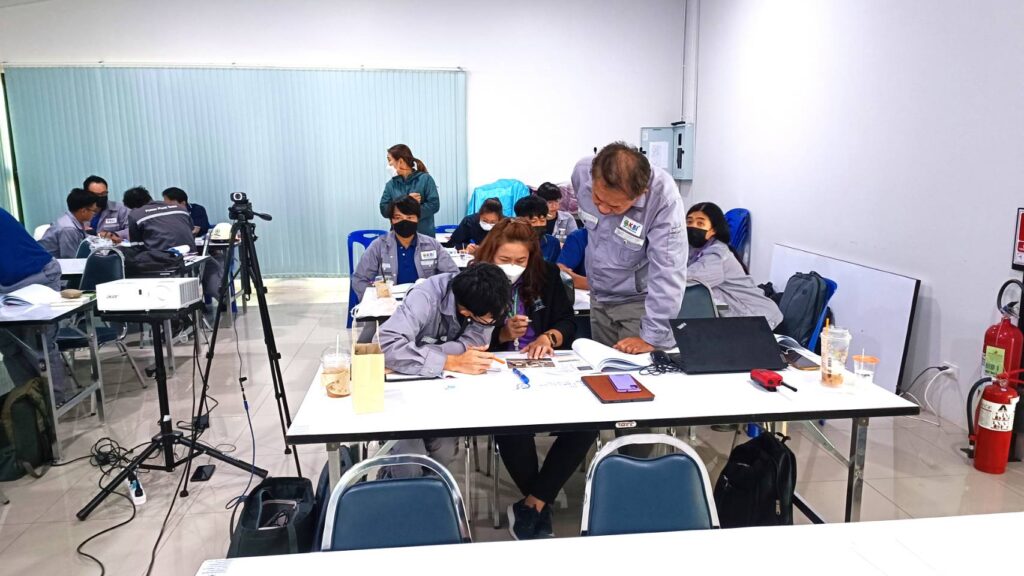
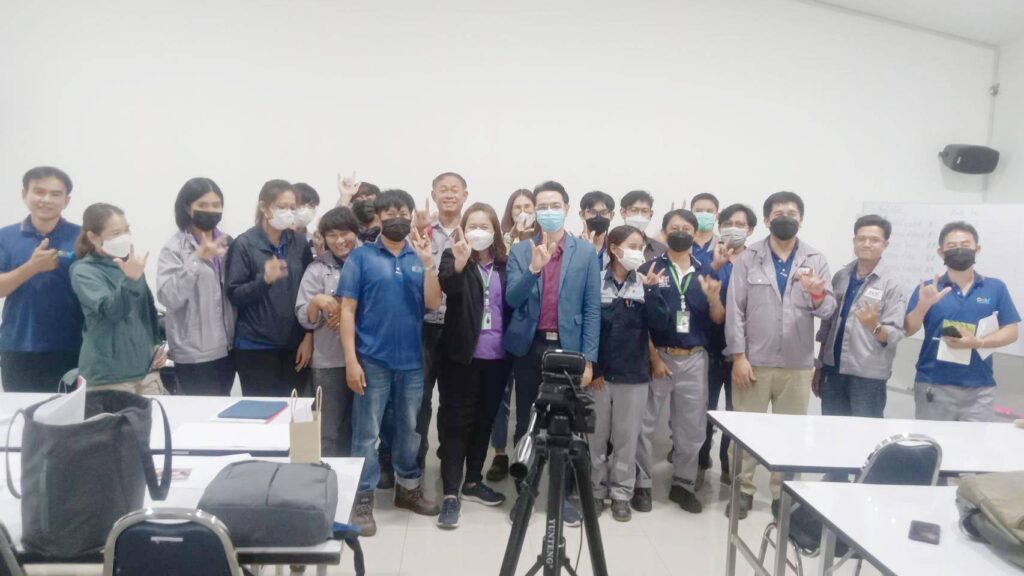